The best method for acrylic engraving.
Acrylic is a commonly used material for laser engraving and laser cutting. Laser engraving and cutting machines allow for quick and precise engraving and cutting of acrylic lamps, various unique signs, various storage boxes, and much more, with a wide range of acrylic engraving designs available.
Acrylic, also known as PMMA (Polymethylmethacrylate), is characterized by its transparency and light transmittance, similar to glass. Acrylic is an early developed and important thermoplastic plastic. It is used in a variety of applications, including acrylic sheets, acrylic artificial stone, acrylic lacquer, and more. Laser engraving on acrylic enables a wide range of creative applications and acrylic engraving products.
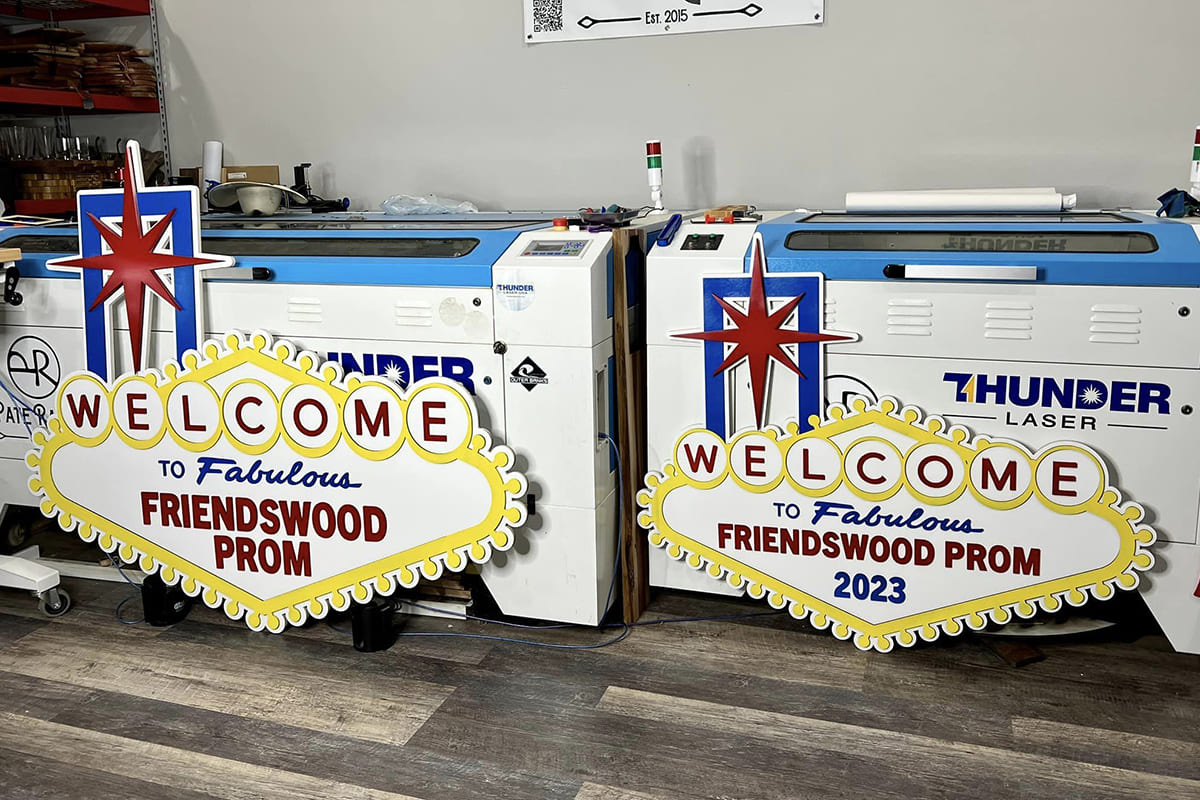
Common Categories:
Depending on the different properties of acrylic, different colors, and visual effects to meet diverse requirements, acrylic can be divided into various categories:
1.Transparency:
Acrylic sheets can be divided into transparent sheets, semi-transparent sheets (including colored transparent sheets), and colored sheets (including black and white sheets and color sheets) according to transparency.
2.Performance:
According to performance, shock-resistant sheets, UV-resistant sheets, standard sheets, and special sheets such as high-impact-resistant sheets, flame-retardant sheets, frosted sheets, metallic-effect sheets, highly abrasion-resistant sheets, light-guide sheets, etc., are available.
3.Manufacturing Process:
Acrylic can be divided into cast sheets and extruded sheets according to the manufacturing process:
Cast sheets: High molecular weight, excellent rigidity, strength, and excellent chemical resistance. These sheets are characterized by flexibility in the color palette and surface texture effects, and they are available in various specifications suitable for various special applications. Cast sheets generally perform better for acrylic engraving and provide overall better results than extruded sheets.
Extruded sheets: Compared to cast sheets, extruded sheets have a lower molecular weight and slightly lower mechanical properties but are more flexible. This facilitates bending and thermoforming. When processing larger sheets, it is advantageous for various rapid vacuum thermoforming processes. At the same time, the thickness of extruded sheets is more tolerant compared to cast sheets (casting: 1.8 mm-300 mm, extrusion: 0.5-12 mm).
Since extruded sheets are produced in mass production and colors and specifications are difficult to adjust, the variety of products is limited, making them ideal for acrylic engraving and more cost-effective than cast sheets.
4.Regenerated Acrylic Sheets:
There are also recycled, regenerated acrylic sheets made from recycled acrylic cuttings. These cuttings are converted into pure MMA (Methylmethacrylate) monomers through thermal decomposition, which are then processed into acrylic sheets through chemical polymerization.
The decomposition monomer obtained through this process is not as pure as the newly synthesized monomer and has lower quality and performance.
Applications of Acrylic Engraving with Laser:

Illuminated (LED) or clear signs

Advertising displays (Point of Sale) made of acrylic

Acrylic engraving awards and trophies

Photo etching or engraving on acrylic

Home accessories made of acrylic

Architectural model making with acrylic

Laser-cut acrylic letters
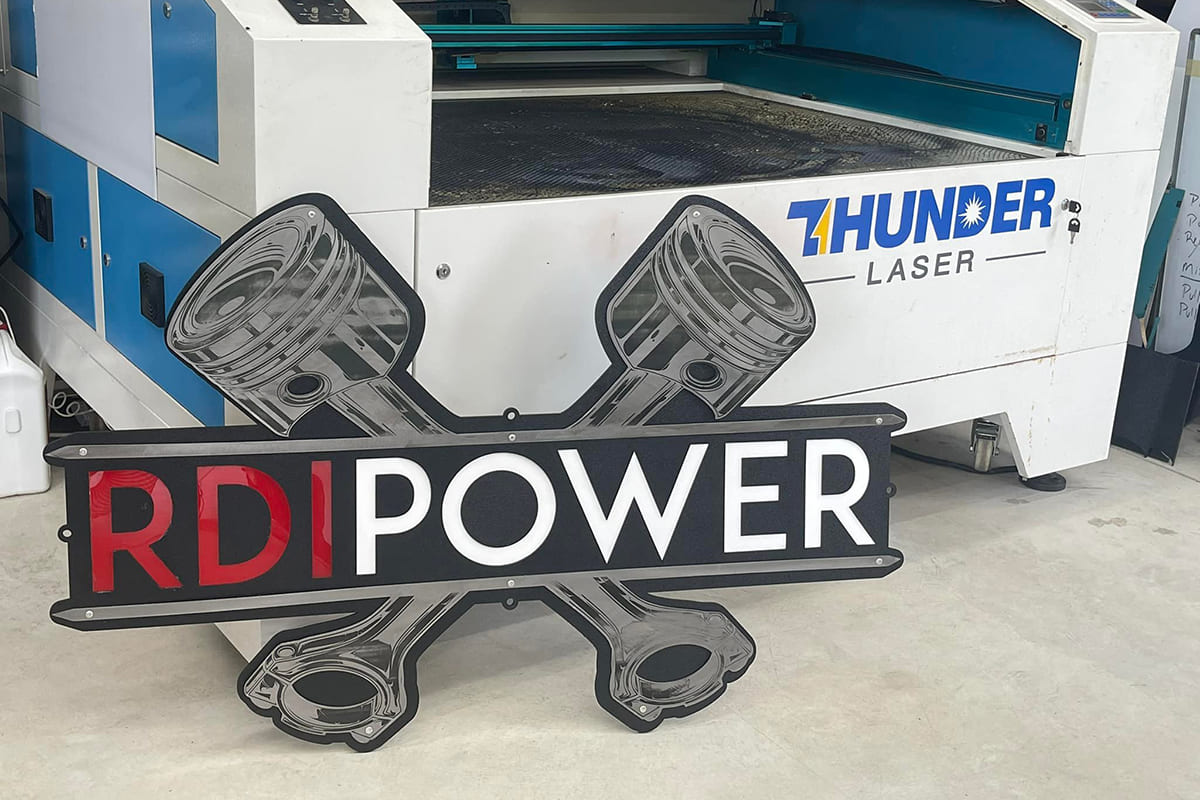
Outdoor or indoor signage
Why Thunder Laser for Your Acrylic Engraving?
The NOVA series from Thunder Laser combines cutting and engraving of acrylic excellently.
The maximum thickness of acrylic that can be penetrated with various laser models mainly depends on the power of the laser tube. The higher the power of the laser tube, the thicker the acrylic that can be cut.
However, the NOVA series stands out with greater laser power and a larger processing platform, including a pass-through door. This gives it a clear advantage in cutting sheet material compared to machines from other brands. Acrylic engraving is thus more precise and faster than ever.
Processing Tips
How to avoid burning during acrylic engraving by laser cutting and laser engraving?
When laser cutting acrylic, there is a risk of ignition if the air pressure is not adjusted to the required level. To prevent this, you can follow these tips for acrylic engraving:
1.Adjust the air pressure to reduce the temperature of the cut and avoid ignition due to high heat during acrylic engraving.
2.Use moist cloths to increase humidity. The evaporating moisture from the moist cloths lowers the temperature during the laser cutting process of acrylic and reduces the risk of ignition during acrylic engraving (structural paper or moist paper, kitchen paper, etc., can be used).
Even when taking these measures for acrylic engraving, you should carefully monitor the laser operation to prevent ignition.
How to avoid laser reflection damage during acrylic engraving?
When laser cutting acrylic with a laser, damage to the back of the material may occur during acrylic engraving when the laser energy penetrates the acrylic, hits the honeycomb bed, and is reflected back onto the acrylic, creating excess and clearly visible marks. To avoid such damage during acrylic engraving, it is important to…
How to reduce laser reflection during engraving acrylic?
1.For smaller cut surfaces, you can use moist cloths to reduce the energy of reflection and protect the acrylic.
2.For larger cuts, you can lift acrylic altogether using nails or other tools to reduce the energy of laser reflection during the back-reflection process and protect the acrylic from damage.
3.Cut the acrylic on the knife holder. Since the knife holder is less dense than the honeycomb bed, less laser energy is reflected back during the cutting process. It is important to cut from the inside out during cutting, which is not suitable for very small parts.

4.Optimize the processing parameters, increase the speed, and reduce the power to minimize the energy reflected back in unit time.
Notes:
Ventilation system.
When cutting acrylic, it is important to use an effective ventilation system. Without a ventilation system, there is a high risk of fire to the material. In addition, the workplace may be filled with inflammable or even explosive gases when cutting acrylic glass. This is dangerous.
If the ventilation system fails, the operator may be exposed to health risks. Or if the machine cover is opened during acrylic processing.
Therefore, it is necessary to check the functionality of the ventilation system, ventilate the workplace, and close the machine cover when cutting acrylic.
Remove the coating.
When contour carving on acrylic, a white layer forms. To remove it, you can use acetone, solvents, or polishing paste.
Be very careful when handling acetone. If you saturate the cloth too much and apply too much pressure, the surface of the acrylic sheet may melt.
Mineral oil is a common and relatively inexpensive product. The risk of melting acrylic during processing is lower than when using acetone.
Use soapy water for engraving. Soapy water can help you achieve a high-quality engraving. You should apply a very thin layer to the material and wait for it to dry. The engraving result will be excellent.
How to store acrylic:
Store the sheets at room temperature and in well-ventilated, dry environments. The sheets should not be exposed to direct sunlight, heat, or moisture.
Before using the sheets, do not remove the protective film, as dust and dirt can adhere to the surface due to electrostatic attraction. The protective film also protects the sheets from wear and scratches.
Avoid warping by storing the sheets flat. If you need to